高温合金材料在航空航天领域的应用
高温合金概述
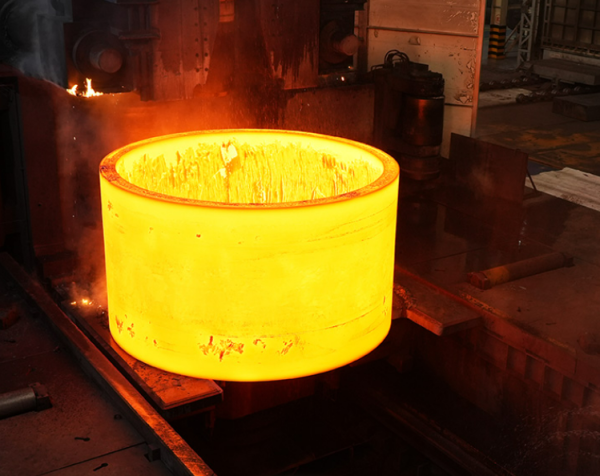
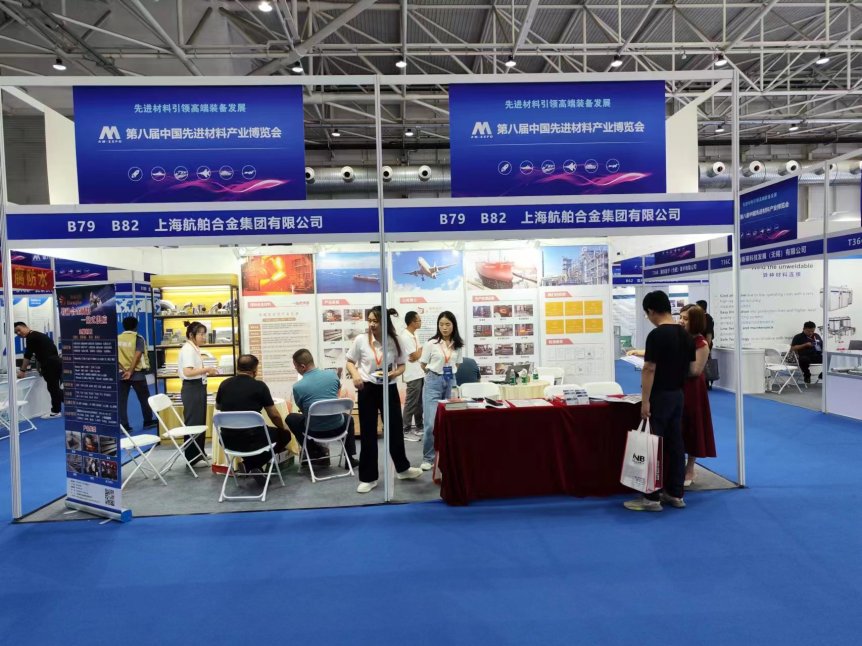
表1 国外高温合金牌号及注册商家
以往高温合金仅以铁、钴、镍为基体,随着技术的发展可以添加不同的合金元素来提升其不同的性能,目前高温合金所涉及的合金元素主要有Fe,Co,Ni,Ti,V,Nb,Ta,Cr,Mo,W,Re,Al,Ce,Y,B等,表2所示为高温合金中的合金元素及其作用。
除了主要的合金元素外,高温合金中还含有 S,Se,Te,As,Sb,Mg,Hf,Zr等多种微量元素,有些微量元素是人为添加,有些则是原料中带来的杂质元素。高温合金中微量元素大致可分为有益元素和有害元素两类,如表3所示.
表3 高温合金中的微量元素
加入高温合金中的十余种合金元素可形成20余种相,这些相可归纳为固溶体、金属间化合物和间隙化合物三大类。
1、固溶体
由于原子尺寸、晶体结构、电子层结构等因素的不同,不同合金元素的固溶度差别很大,每个元素在高温合金中的溶解度与其在二元合金中的溶解度相差也较大。高温合金的基体是面心立方 Y固溶体,构成这种奥氏体基体的元素主要有 Ni,Co,Fe,Cr,Mo,W 等。
2、金属间化合物
高温合金常见的金属间化合物几乎都是过渡族金属元素之间的化合物,按晶体结构可以分为几何密排 (GCP)相和拓扑密排(TCP)相两大类。
①GCP相:
晶体结构都是由密排面按不同方式堆垛而成,只是 由于密排面上A原子和B原子的有序排列方式不同而密排面的堆垛方式不同,形成了多种不同的结构,这些相的配位数为12,分子式为B3A,B为 Mn,Fe,Co,Ni等元素,A指原子半径较大的Ti,V,Cr各族元素。
②TCP相:
原子排列比等径球体的最密排列还要紧密,配位数达到14~16,原子间距极短。为了得到较高的空间利用率,TCP相要求由两种大小不同的原子组成,得到全部或主要为四面体堆垛结构。在高温合金中常见的TCP相有B2A型的Laves相、BA型的σ相、B7A6型的μ相,其中A通常指周期表中的Ti,V, Cr各族元素 ,B指 Fe,Co,Ni等元素。
3、间隙化合物
过渡族元素常与C,N,B等元素形成碳化物、氮化物和硼化物等间隙相。其晶体结构特点是金属原子尽可能密排,而原子半径小的C,N和 B原子位于金属原子的间隙中。间隙相按晶体结构可分为八面体间隙相、三棱柱间隙相和复杂结构间隙相三类。在高温合金中 Ti,V,Nb,Ta,Zr,Hf等元素的碳化物属于八面体间隙相,M3C和M7C3属于三棱柱间隙相,M6C和 M23C6属于复杂结构间隙相。
间隙相大多以固溶体的形式存在。不仅金属原子可以互相取代,C,N,B原子也可以相互部分取代。高温合金中MC型碳化物的金属原子“M”是由不同比例的 Hf,Zr,Ta, Nb,Ti,V等元素组成,而TiC常常由于C被部分N取代形成Ti(CN)。
高温合金中还存在四方晶体结构的M3B2硼化物和六方结构的M2SC碳化硫物等两种间隙相。
(a)涡轮发动机实物图
(b)涡轮发动机结构示意图
高温合金具有较高的热稳定性和热强度,能在高温下具有良好的抗腐蚀、抗氧化能力,是制造航空涡轮发动机热端部件必不可少的关键材料,主要应用于制造发动机涡轮热端部件,即涡轮盘、涡轮导向叶片、涡轮工作叶片、燃烧室和加力燃烧室的各种零部件。在现代先进的航空发动机中,高温合金材料用量占发动机总量的40%-60%。
燃烧室是发动机各零部件中工作温度最高的区域,燃烧室内燃气温度达到1500-2000℃时,室壁合金承受温度可达 800~900℃,局部可达1100℃。用作燃烧室的合金承受急热急冷的热应力和燃气冲击力作用,特别是在起飞、加速和停车时,温度变化更为急剧。由于周期循环加热冷却,燃烧室常出现变形、翘曲、边缘热疲劳裂纹等。
近年来,燃烧室采用的高温合金大部分是固溶强化型合金,合金中含有大量 W,Mo,Nb等固溶强化元素,高温强度高,成形焊接性能良好,具有代表性的牌号有GH1140、GH3030、GH3039、GH3333、 GH3018、GH3022、GH3044、GH3128、GH3170等 。
导向叶片是调整从燃烧室出来的燃气流动方向的部件,也称导向器,是涡轮发动机上受热冲击大的零件之一,尤其是当燃烧室内燃烧不均匀、工作不良时,导向叶片所受热负荷更大,先进涡轮发动机导向叶片工作温度可达1100℃。由热应力引起的扭曲、由温度剧烈变化引起的热疲劳裂纹及局部烧伤是导向叶片在工作中的主要缺陷。
用作导向叶片的合金,大多数采用精密铸造工艺生产,合金中可以加入较多的 W, Mo,Nb,Al,Ti等固溶强化和时效强化元素,且合金中C,B含量也比变形高温合金高。有些导向叶片也采用时效强化的板材直接焊接而成。先进的航空发动机多采用空心铸造叶片,其冷却效果好,可以提高使用温度。国内导向叶片合金的使用温度可达000~1050℃, 代表性精密铸造合金有K214,K233,K406,K417,K403,K409,K408,K423B等。
随着发动机的发展,为满足发动机涡轮盘温度的进一步提高,导向叶片的结构也发生变化,尝试采用GH5605和GH5188。变形高温合金板材焊接的层板结构作为导向器叶片。
涡轮叶片是航空发动机中工作条件最恶劣的部件,工作环境温度高,转动时承受很大的离心应力、振动应力、热应力、气流冲刷力等,叶身部分承受拉应力大约140MPa,叶根部分承受平均应力为 280-560MPa,叶身和叶根部分承受温度分别为650-980℃和760℃左右。先进航空发动机的燃气进口温度已达1380℃,推力达226kN。典型牌号有 GH4033,GH4037,GH4143,GH4049,GH4151,GH4118,GH4220等,可在750-950℃使用。在新机研制和老机种改性时,都选用铸造高温合金制造涡轮叶片。铸造合金典型的牌号有K403,K417, K417G,K418、K403、K405、K4002等。
涡轮盘在航空发动机部件中所占质量最大,单件质量在50kg以上,大型涡轮盘单件质量达到几百 千克。涡轮盘工作室,一般轮缘温度可达550-650℃,而轮心温度只有约300℃,整个涡轮盘温差很大。因此,会产生较大径向的热应力。涡轮正常转动时带着涡轮叶片高速旋转,承受很大的离心力,榫齿部分所受的应力更为复杂,既有拉应力,又有扭曲应力,在起动和停车过程中构成一次大应力低周疲劳。
涡轮盘用变形高温合金,一类为铁镍基高温合金,典型的合金牌号有GH2132, GH2135,GH2901,GH4761等,工作温度在650℃以下;另一类为镍基高温合金,典型牌号有GH4196,GH4133,GH4133B,GH4033A,GH4698等,使用温度可达 700^800℃。
运载火箭是把各种航天器送入空间轨道的运载工具 ,高温合金在航天领域主要应用于推力运载火箭发动机上 。图2是液体燃料火箭发动机实物及其结构示意图,是将推进剂储箱或运载工具内的反应物(推进剂)变成高速射流而产生推力,由图(b)可看出,火箭发动机喷嘴处气流达到 2500m/s,温度高达1350℃。
火箭发动机用高温合金原则上都可以采用航空涡轮发动机用合金,但对比航空发动机,火箭发动机用材还有一些新 的特点 :
①火箭发动机燃料箱、泵传送器等部件工作是在以液氧一煤油或液氢一液氧以及作为氧化剂的发烟硝酸和四氧化氮特殊介质中使用,具有特别强烈的侵蚀性。除了在1000℃以上的工作温度下出于腐蚀而引起的问题之外,流过的气态燃烧产物也产生冲蚀性,因此,所需材料不仅要求高温化学稳定性好,还需要适应低于-253℃的低温环境。
②火箭启动时从零到满载时间极短,一般只需0.2-0.5s,其加速度是5-6倍于地球的引力加速度,由于加速度增高引起的高度过载会对材料施加巨大的机械负荷,所以,要求充分考虑材料的热冲击和热膨胀问题。
③由于常规火箭涡轮一次性使用,所以一般对材料的持久强度和热疲劳强度要求较低。
④火箭本身重量必须尽可能的小,因此,金属材料的比强度在火箭制造中具有特别重要的意义。
⑤弹道火箭进入大气层时,热流量为10000-25000kca1/(m2"s)(lkca1=4186J),在短时间内引起巨大的温度梯度,长时间作用则会建立起平衡温度,因此,对金属材料的耐热性有特殊要求。
铸造高温合金是由合金锭重熔后直接浇注或定向凝固成零件的高温合金,其发展始于20世纪40年代。铸造高温合金不再考虑锻造变形性能,可通过精密铸造方法或定向凝固工艺铸造出形状复杂且有通畅内腔的无余量空心薄壁叶片。因此,铸造高温合金元素总量要显著高于变形高温合金,其 中,固溶强化元素增添了Re,Ru等元素,难熔金属元素W的含量提高(有些合金超过10%)沉淀强化合金元素除Al,Ti之外,还加入Nb,Ta,Hf,V等元素。
铸造高温合金按凝固方法分类可分为等轴晶铸造高温合金、定向凝固柱晶高温合金和单晶高温合金三类。
在一般条件下铸造高温合金时,熔融的合金在铸型中逐渐冷却,由多个晶核产生多个晶粒,随着温度降低 ,晶粒不断长大,最后充满整个零件。由于合金冷却时散热的方向未加控制,晶粒长大也是任意的,得到的晶粒形状近似球形,称为等轴晶铸造高温合金。
等轴晶铸造高温合金晶界上往往存在许多杂质和缺陷,是最薄弱的易破坏区域。采用细晶铸造工艺虽然能在一定程度上改善铸造高温合金的持久强度和疲劳性能,但是无论如何净化晶界或提高晶界强度,始终不能改变晶界作为最薄弱环节的事实。且对于铸造的构件,在同一铸件内力学性能都有可能不同,如整体铸造的涡轮盘,在轮毂和叶片剖面之间晶粒度差别很大,热处理期间叶片会变脆。相对于定向凝固高温合金,等轴晶铸造高温合金制作方法简单,成本低,因此,其在高温合金领域得以快速发展及应用。
定向凝固高温合金是通过定向凝固技术制备出晶界平行于主应力轴从而消除有害横向晶界的柱状晶高温合金。为达到定向凝固的目标,在整个合金结晶过程中必须满足两个基本条件:一是在整个凝固过程中,铸件的固一液相界面上的热流应保证从一个方向扩散,即定向散热;二是结晶前沿区域内必须维持正向温度梯度,以阻止形成新的晶核。
图3为Bridgman定向凝固和整套装置示意图,定向凝固时液态金属注入壳型,首先与水冷铜板相接触,由于板面温度很低,靠近板面的那一层液态金属迅速冷却到结晶温度以下并开始结晶,此时形成的晶粒位向紊乱,随后的凝固过程中由于热流通过已结晶的固态金属有方向地向冷却板散热,且结晶前沿存在着正向温度梯度,具有<100>方向的晶粒择优长大,排挤其他方向的晶粒,只要凝固条件维持不变 ,柱状晶就可以维持生长,直到整个叶片。定向凝固工艺用于飞机涡轮盘制备中,在涡轮盘的横截面上会形成指向盘心部的柱状晶,如图4所示。制备定向凝固柱状晶高温合金的方法有很多,如用发热剂控制晶粒按<100>方向优先长大的发热铸型法;通过功率来控制晶粒长大的功率降低法(PD法);用可移动水冷铜板和铸型及增设辐射挡板来实现低功率方法来控制晶粒长大的快速凝固法(HRS法);用液态金属 (如热锡槽)以冷却铸型进行导热方式控制晶粒长大的液态金属冷却法(LMC法)等。目前应用最为广泛的是快速凝固法。
变形高温合金是指将铸锭进行冷、热加工制成各种型材或零件毛坯,最后制成热端零件的高温合金,其关键是合金锭具有成形能力。与铸造高温合金相比,变形高温合金合金化程度低,因此,熔点较高,热加工温度上限较高 ,合金再结晶温度较低,降低热加工温度下限,因此,变形高温合金热加工范围较铸造高温合金宽。按基体元素的不同,变形高温合金可分为铁基变形高温合金、镍基变形高温合金和钴基 变形高温合金。
铁基变形高温合金是从奥氏体不锈钢发展起来的。铁基变形高温合金Fe含量在18%~45%,为稳定奥氏体,通常要加入25%-45%的元素Ni,也可加入适量的元素Mn,N,C。代替部分元素 Ni。为保证合金有充分的抗氧化腐蚀能力,铁基变形合金中还加入11%~23%的元素Cr,所以铁基高温合金实际上是以 Fe-Ni-Cr三元系为基,当Ni含量大于40%时一般也称作铁镍基高温合金。铁基高温合金的基体通常有 Fe-15Cr-25Ni型、Fe-15Cr-35Ni型、Fe-15Cr-45Ni型。常用铁基变形高温合金的 牌号、化学成分及使用温度如表4所示。
表4 常用铁基变形高温合金的牌号、化学成分及使用温度
铁基变形高温合金按其强化方式可分为三类 :第一类是碳化物、氮化物或复合碳氮化物强化合金,其使用温度在 550-600℃,现已逐渐被其他合金取代;第二类是固溶强化合金,在高温下有良好的抗氧化和抗腐蚀能力,使用温度在 800-950℃,主要用作板材,制造承力不大但工作温度较高的零件;第三类是金属间化合物强化合金,使用温度在600-750℃表5为部分铁基高温合金在高温下的力学性能。
表5 铁基变形高温合金高温力学性能
镍基变形高温合金通常加入10%-25%的Cr元素,以保证合金具有良好的抗氧化腐蚀性能,所以镍基合金实际上以 Ni-Cr为基体。此外,有些合金在Ni-Cr固溶体中加入元素 Co(15%-20%),Mo(约15%)或 W(约11%),分别构成以 Ni-Cr-Co,Ni-Cr-Mo,Ni-Cr-W为基体的三元系变形高温合金。表6为我国常用镍基变形高温合金的牌号、化学成分及使用温度。图6为在涡轮叶片和盘片上,高温合金应用的发展趋势。
表6 中国常用镍基变形高温合金的牌号、化学成分和使用温度
图6 高温合金在叶片和盘片上应用的发展趋势和对比
镍基变形高温合金固溶强化元素种类多,沉淀强化元素 AI+Ti含量高,具有较好的组织稳定性。与铁基和钻基变形高温合金相比,镍基变形高温合金具有良好的抗氧化、抗热腐 蚀和抗冷、热疲劳性能,塑性、高温蠕变强度优异,使用温度可达800℃以上。表7为常用镍基变形高温合金高温力学性能。
表7 镍基变形合金的高温力学性能
钴基变形高温合金实质上是以Co-Ni-Cr三元系为基,另含 W,Mo,Nb,Ta等固溶强化元素和碳化物形成元素。表8为有代表性的钴基变形高温合金的化学成分。
表8 部分钻基变形高温合金的化学成分(质量分数)
钴基变形高温合金与镍基变形高温合金相比,其加工硬化速率较大,零件成形后的表面质量较好,但在成形过程中,一般需要较多的热加工加热火次或冷变形中间退火次数,其加 工成形设备的吨位也要求较大。钴基变形高温合金在高于 980℃时,其强度很高,抗热疲劳、热腐蚀和耐磨腐蚀性优异,但是,钴基变形高温合金以碳化物为主要强化相,缺少共格类的强化相,在较低和中等温度范围内持久强度比镍基变形高温合金低。表9列出了有代表性的钴基变形高温合金的高温力学性能。
表9 钻基变形高温合金高温力学性能
随着高温合金工作温度和强度的不断提高以及综合性能的改善,合金中强化元素含量不断增加,成分越来越复杂,热加工性能变得很差,不少高性能镍基高温合金已不能热加工变形,只能以铸态使用。然而,由于铸造组织偏析严重导致了显微组织的不均匀和力学性能的波动,故而开始采用粉末冶金工艺生产高温合金克服上述缺点,得到几乎无偏析、组织均匀、热加工性能良好的高温合金材料。粉末高温合金是先进航空发动机关键热端部件的优选材料,主要用于制造涡轮盘、压气机盘、鼓筒轴、涡轮盘、高压挡板等发动机热端高温承力转动部件。
目前,用粉末冶金法制得的高温合金可分为普通粉末 (powdermetallurgy, PM)高温合金和氧化物弥散强化 (oxidedispersionstrengthened,ODS)高温合金两类。
典型的第三代粉末高温合金有Honeywell开发的 Alloy10,NASA/GE/P&-WA合作开发的Renel04(ME3)等。法国在N18基础上研发的NR3,NR6,N19等合金也属于第三代粉末高温合金。美欧研发的粉末高温合金成分及合金特性如表10所示。
高熵合金由五种或五种以上主要元素组成,每种元素的原子百分比介于5%-35%。高熵合金虽然组成元素复杂,但其一般容易形成一些简单结构的晶体,如面心立方结构等。高熵合金制备工艺简单、价格低廉,在科学研究和实际应用方面具有极大的潜力。高熵合金具有高强度、高硬度、较好的拉伸和压缩性能、耐磨,耐腐蚀和耐氧化等特点,可以用 于制备工业生产以及日常生活中的各类模具、工具等 ;高熵合金具有高硬度、高强度、耐磨性和较低的弹性模量等特点 ,可以用于制备轧制辊筒的硬面、高尔夫球杆的球头以及其他运动器械等;高熵合金具有耐高温和高强度等特点,可以用于制备焊接材料、涡轮叶片、高温设备的耐热部件和热交换器等;高熵合金具有比不锈钢等耐腐蚀材料更优异的耐腐蚀性、耐氧化性、抗压强度和耐高温性等特点,可以用于制备耐腐蚀容器、船体材料和航空航天材料等;此外高熵合金还具有一些特殊的电、光、磁和热效应,可以用于制备电子元件、发电机中的磁元件和高频变压器等。
到目前为止已经研究出了有很多种适合高熵合金的制备方法,如真空熔炼法、激光熔覆法、机械合金化法、粉末冶金法等。高熵合金涂层主要采用电化学法、热喷涂法、磁控溅射法等技术制备。
当前,具有代表性的高熵合金主要以过渡金属(如 Cr,Fe,Ni,Co,Cu,Mn)或难熔金属(如V,Nb,Cr,Ta,W,Mo,Hf,Ti,Zr)为主要元素。高熵合金与常规结构材料力学性能之比较,如图9-图11所示。高熵结构的新型合金较于传统结构金属,具有更加优异的比强度 、加工硬化率、比屈服强度等力学性能。
本站部分文字及图片来源于网络,版权归原创者所有,如有侵权请及时通知我们。